1. Introduction
In any industrial project, proper welding techniques are of utmost importance for ensuring both efficiency and safety. The skilled labor supply and manpower recruitment are crucial components in achieving the desired results. With the help of a trusted labor hire agency and industrial workforce solutions, companies can find the right talent for their welding and fabrication needs. In this blog, we will explore the importance of proper welding techniques in enhancing efficiency and safety in industrial projects. From the benefits of temporary staffing services to the role of manpower outsourcing, we will delve into the various aspects of labor management and how it contributes to successful project completion. Join us as we uncover the best practices in the field of welding and the integral role of skilled labor supply, recruitment, and technical works.
2. The impact of proper welding techniques on efficiency in industrial projects
Proper welding techniques have a significant impact on the efficiency of industrial projects. When welding is done correctly, it ensures that the joints are strong and durable, reducing the chances of rework or repairs. This, in turn, leads to increased productivity and cost-effectiveness. Welding techniques such as TIG (Tungsten Inert Gas) welding and MIG (Metal Inert Gas) welding allow for precise control, resulting in smooth and clean welds.
Efficiency is also enhanced through the use of advanced welding equipment and technology. Automated welding systems and robotic welders can perform complex tasks with speed and accuracy, reducing the time required for project completion. Furthermore, proper welding techniques create efficient workflows, as well-trained welders can complete tasks efficiently, while also ensuring the quality of their work.
By prioritizing proper welding techniques, industrial projects can maximize their efficiency, minimize downtime, and ultimately achieve successful outcomes. In the next section, we will explore the impact of these techniques on safety in industrial projects. Stay tuned to learn more about the crucial role of welding techniques in ensuring a safe work environment.
3. The significance of proper welding techniques for safety in industrial projects
In addition to enhancing efficiency, proper welding techniques also play a crucial role in ensuring the safety of workers and the overall success of industrial projects. Welding can be a hazardous process, involving high temperatures, intense light, and toxic fumes. Utilizing the correct welding techniques helps minimize the risk of accidents and injuries.
One key aspect of safety in welding is proper ventilation and fume extraction systems. Welding generates various hazardous gases and vapors, including ozone, nitrogen oxides, and hexavalent chromium. These fumes can be detrimental to the health of workers if inhaled. By employing effective ventilation systems, these harmful substances can be removed from the work area, protecting the health of the welding personnel.
Proper technique also ensures weld integrity, reducing the likelihood of structural failure. Welds that are not performed correctly can result in weak joints, which may lead to accidents or equipment malfunction. By following proper procedures and using appropriate equipment, welders can create high-quality welds that withstand the stresses and strains of industrial applications, ultimately increasing safety.
Furthermore, proper welding techniques involve adequate training and certification for welders. Skilled and knowledgeable welders are better equipped to identify potential risks, troubleshoot problems, and ensure that safety protocols are followed. By investing in comprehensive training programs and certifications, industrial projects can establish a culture of safety that permeates every welding operation.
In conclusion, proper welding techniques are essential for ensuring the safety of workers and the success of industrial projects. By employing effective ventilation systems, maintaining weld integrity, and investing in training, companies can create a safer work environment and minimize the risks associated with welding. In the next section, we will discuss some common welding mistakes to avoid in order to enhance both efficiency and safety. Stay tuned for valuable insights into avoiding potential pitfalls in welding projects.
4. Common welding mistakes and their effects on efficiency and safety
In order to enhance both efficiency and safety in welding projects, it is crucial to be aware of and avoid common welding mistakes. These mistakes can have significant impacts on the overall quality of the weld and the safety of the workers involved.
One common mistake is improper cleaning and preparation of the welding surface. Failing to remove dirt, rust, or paint can affect the weld’s integrity, leading to weak joints and potential failures. Additionally, inadequate beveling and chamfering can compromise the weld’s strength, resulting in reduced structural integrity.
Another common mistake is improper electrode selection. Different electrodes have varying properties and are suited for specific welding applications. Using the wrong electrode can lead to poor weld quality, reduced consistency, and compromised safety.
Insufficient heat control is also a frequent mistake that can negatively impact both efficiency and safety. Applying too much heat can cause distortion, warping, and even burn-through, while insufficient heat can result in incomplete penetration and weak joints.
Finally, neglecting to address welding position and technique can lead to significant issues. Welders must be skilled in various welding positions and techniques, such as vertical or overhead welding, to ensure uniform and strong welds.
By being aware of these common welding mistakes, companies can take proactive measures to prevent them from occurring. Proper training, regular inspections, and quality control measures can help ensure that welders adhere to correct practices, enhancing efficiency and safety in industrial projects. Stay tuned for practical tips on how to avoid these common mistakes in the next section.
5. Training and certification for proper welding techniques
To ensure the proper execution of welding techniques and to improve efficiency and safety in industrial projects, it is essential for welders to receive comprehensive training and certification.
Proper training provides welders with the knowledge and skills necessary to perform welding tasks effectively. It covers topics such as welding theory, equipment operation, safety protocols, and specific welding techniques for different materials and applications. Moreover, training programs often include hands-on practice, where welders can refine their skills under the guidance of experienced instructors.
Obtaining certification is equally important, as it validates a welder’s competency and adherence to industry standards. Certification bodies, such as the American Welding Society (AWS) or the International Institute of Welding (IIW), assess welders based on their knowledge, skills, and ability to produce high-quality welds. These certifications not only serve as proof of a welder’s expertise but also demonstrate a commitment to professionalism and safety in welding projects.
Employers should prioritize investing in training and certification programs for their welders. By doing so, they can ensure that their workforce is equipped with the necessary skills and knowledge to perform their tasks efficiently and safely. Moreover, companies that prioritize training and certification often see improved productivity and reduced incidents, as well as increased customer satisfaction due to the consistently high quality of their welds.
In the next section, we will explore the benefits of utilizing advanced welding technologies to further enhance efficiency and safety in industrial projects.
6. The role of advanced technology in enhancing welding efficiency and safety
In today’s rapidly evolving industrial landscape, advancements in technology have revolutionized the welding industry, offering new tools and techniques to enhance efficiency and safety in industrial projects. As companies strive to stay competitive and meet increasingly complex project requirements, it is essential to embrace these innovative technologies.
One such advancement is the use of automated welding systems. These systems utilize robotics and computer-controlled machinery to perform welding tasks with precision and consistency. By eliminating human error and variability, automated welding systems can significantly improve weld quality and reduce the need for rework. Additionally, these systems can operate in hazardous environments, reducing the risk of accidents for human welders.
Another technology that has gained popularity is laser welding. Laser welding uses a high-energy beam of light to join materials together. This technique offers several benefits, including faster welding speeds, reduced heat input, and increased control over the welding process. Moreover, laser welding is particularly suited for precise and intricate welding tasks, making it ideal for industries such as automotive, aerospace, and electronics.
Furthermore, advancements in welding equipment, such as the development of more robust and efficient welding machines and power sources, have contributed to enhanced welding efficiency. These modern machines offer improved arc characteristics, higher duty cycles, and greater control over welding parameters. As a result, welders can achieve better weld quality in less time, leading to increased productivity and overall project efficiency.
Lastly, the integration of data management and monitoring systems into welding processes has also proven to be invaluable. These systems allow for real-time tracking and analysis of welding parameters, ensuring that weld quality remains consistent throughout a project. Additionally, data management systems enable better documentation and traceability of welds, which is crucial for quality assurance and compliance purposes.
By embracing these advanced technologies, companies can optimize welding processes and drive efficiency and safety in their industrial projects. However, it is important to note that while these technologies offer many advantages, proper training and certification are still fundamental in utilizing them effectively. Qualified welders who possess the necessary knowledge and skills, coupled with the utilization of advanced technologies, can create a winning combination that maximizes efficiency, minimizes costs, and ensures the highest standards of safety in welding projects.
In the following section, we will discuss the importance of ongoing maintenance and quality control in welding projects to further enhance efficiency and safety.
7. Case studies demonstrating the benefits of proper welding techniques
To fully understand the importance of proper welding techniques in enhancing efficiency and safety in industrial projects, it is beneficial to examine real-life case studies. These case studies provide tangible examples of how implementing the right welding practices can yield significant improvements in project outcomes.
One such case study involves a construction company that adopted automated welding systems for their pipeline installation projects. Before incorporating automation, the company had to deal with inconsistencies in weld quality, leading to frequent rework and delays. By implementing automated systems, they were able to achieve consistent and high-quality welds, reducing rework by 50% and completing projects ahead of schedule.
In another case, an aerospace manufacturer switched to laser welding for their intricate and critical component assembly. This change allowed them to achieve precision welds with minimal distortion and reduced heat-affected zones. As a result, they experienced improved structural integrity, reduced material waste, and increased productivity.
Moreover, a metal fabrication company utilized advanced welding machines and data management systems to enhance their quality control processes. By closely monitoring welding parameters in real-time, they were able to detect deviations and make immediate adjustments, preventing weld defects and ensuring compliance with industry standards. This resulted in improved product quality, reduced scrap, and enhanced customer satisfaction.
These case studies demonstrate the direct impact of proper welding techniques on project outcomes. By embracing advanced technologies, companies have not only improved efficiency and productivity but also prioritized safety and quality. The implementation of automated systems, laser welding, advanced equipment, and data management systems has proven to be key in achieving these positive results.
In the next blog section, we will discuss the essential role of proper training and certification for welders to ensure the successful implementation of proper welding techniques.
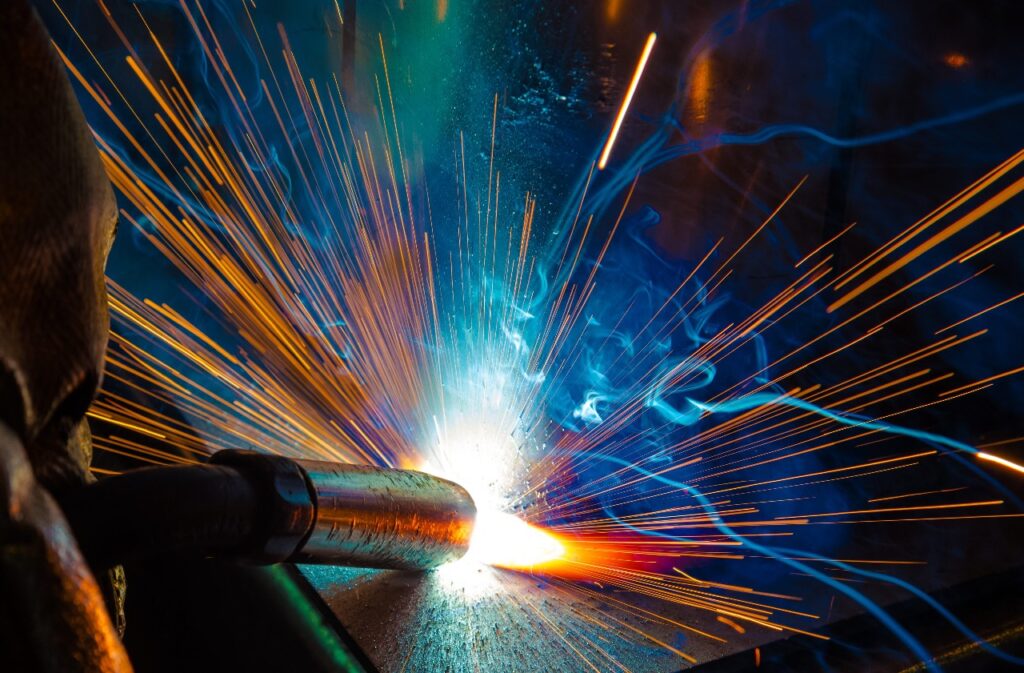
8. Conclusion and the future of welding techniques in industrial projects
In conclusion, the benefits of proper welding techniques in industrial projects cannot be overstated. This blog section highlighted the positive outcomes that can be achieved through the adoption of advanced technologies and the implementation of proper welding practices. Real-life case studies have demonstrated the significant improvements in project efficiency, safety, and quality that can result from using automated systems, laser welding, advanced equipment, and data management systems.
However, it is important to note that the successful implementation of proper welding techniques relies heavily on the skills and knowledge of welders. In the next blog section, we will discuss the essential role of proper training and certification for welders. By investing in training programs and ensuring that welders possess the necessary certifications, companies can further enhance the effectiveness of proper welding techniques and ensure the continued success of their industrial projects.
Looking ahead, the future of welding techniques in industrial projects is promising. With advancements in technology, such as the Internet of Things (IoT) and artificial intelligence (AI), we can expect even greater automation, precision, and efficiency in welding processes. These innovations are set to revolutionize the industry, benefiting not only large-scale industrial projects but also smaller-scale applications.
Stay tuned for the next blog section, where we will delve into the importance of proper training and certification for welders and explore how they contribute to the successful implementation of proper welding techniques in industrial projects.